Description
The Manufacturing Demonstration Facility (MDF) is a 110,000 sq. ft. facility housing integrated capabilities that drive the development of new materials, software, and systems for advanced manufacturing. From binder jetting to 3D tomography to in situ monitoring, the facility leverages a range of equipment and expertise focused on reducing the carbon footprint of the manufacturing sector, efficiently utilizing abundant and available domestic energy resources, and supporting the production of clean energy products that boost the nation’s economy.
This facility has various equipment for the biomaterial development and advanced manufacturing. The equipment include drying oven (for biomass resource and polymer), hammer mill (for biomass resource pre-processing), shredder, compounding mixer (for biomaterial fabrication), twin-screw extruder, compression molder, injection molder, dog-bone sample cutter, large-scale 3D printer, etc.
This facility has various equipment for the biomaterial characterization. The material characterization equipment include differential scanning calorimetry (DSC), thermogravimetric analysis (TGA), tensile property tester, dynamic mechanical analysis (DMA), scanning electron microscopy (SEM), Fourier trans-form infrared (FT-IR), water contact angle machine, rheometer, X-ray Computed Tomography (XCT), etc.
Capability Bounds
Large-scale 3D printer: capable of printing up to 8’ × 6’ × 20’ and of extruding biomaterials 80 lbs per hour
Unique Aspects
Our Biomaterial Development and Advanced Manufacturing capabilities are readily accessible to academic researchers and industrial partners seeking innovative large-scale additive manufacturing solutions. We welcome collaborations and inquiries from diverse sectors interested in harnessing our cutting-edge technologies for biomaterial innovation and manufacturing advancements.
Availability
The Manufacturing Demonstration Facility (MDF) is one of the DOE’s designated user facilities focused on performing early-stage research and development to improve the energy and material efficiency, productivity, and competitiveness of American manufacturers. Research focuses on manufacturing analysis, composites and polymer systems, large-scale systems, and robotics and automation.
Benefit
The Manufacturing Demonstration Facility (MDF) is one of the DOE’s designated user facilities focused on performing early-stage research and development to improve the energy and material efficiency, productivity, and competitiveness of American manufacturers. Research focuses on manufacturing analysis, composites and polymer systems, large-scale systems, and robotics and automation.
Capability Expert(s)
Oluwafemi Oyedeji, Xianhui Zhao
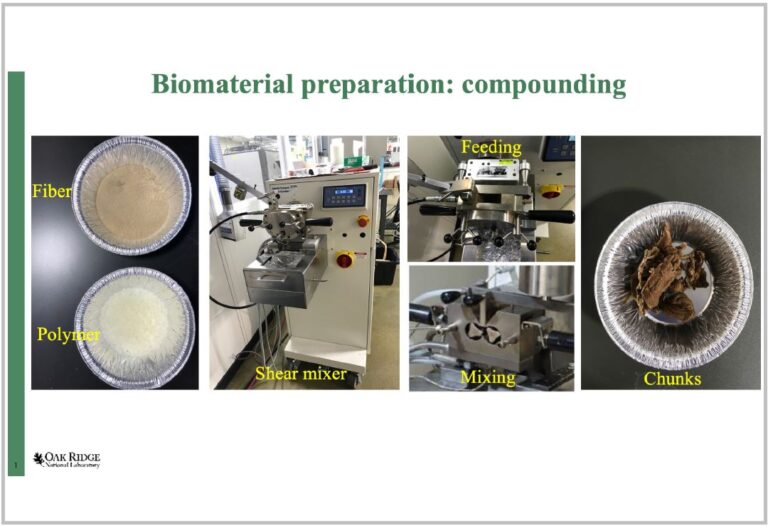
References
1. K. Armstrong, D. Kamath, X. Zhao, M. Rencheck, H. Tekinalp, M. Korey, D. Hun, S. Ozcan. Life cycle cost, energy, and carbon emissions of molds for precast concrete: Exploring the impacts of material choices and additive manufacturing. Resources, Conservation & Recycling. 197: 107117, 2023.
2. X. Zhao, O. Oyedeji, E. Webb, S. Wasti, S. Bhagia, H. Hinton, K. Li, K. Kim, Y. Wang, H. Zhu, U. Vaidya, N. Labbe, H. Tekinalp, N. Gallego, Y. Pu, A. Ragauskas, S. Ozcan. Impact of biomass ash content on biocomposite properties. Composites Part C: Open Access. 9: 100319, 2022.
3. X. Zhao, K. Li, Y. Wang, H. Tekinalp, A. Richard, E. Webb, S. Ozcan. Bio-treatment of poplar via amino acid for interface control in biocomposites. Composites Part B: Engineering. 199: 108276, 2020.
4. X. Zhao, K Li, Y. Wang, H. Tekinalp, G. Larsen, D. Rasmussen, R. Ginder, L. Wang, D. Gardner, M. Tajvidi, E. Webb, S. Ozcan. High-strength polylactic acid (PLA) biocomposites reinforced by epoxy-modified pine fibers. ACS Sustainable Chemistry & Engineering. 8 (35): 13236-13247, 2020.
5. X. Zhao, H. Tekinalp, X. Meng, D. Ker, B. Benson, Y. Pu, A. Ragauskas, Y. Wang, K. Li, E. Webb, D. Gardner, J. Anderson, S. Ozcan. Poplar as biofiber reinforcement in composites for large-scale 3D printing. ACS Applied Bio Materials. 2 (10): 4557-4570, 2019.
6. M. Korey, M. Rencheck, H. Tekinalp, S. Wasti, P. Wang, S. Bhagia, R. Walker, T. Smith, X. Zhao, M. Lamm, K. Copenhaver, U. Vaidya, S. Ozcan. Recycling polymer composite granulate/regrind using big area additive manufacturing. Composites Part B: Engineering. 256: 110652, 2023.
7. M. Rencheck, M. Korey, X. Zhao, H. Tekinalp, S. Ozcan. Towards the applications for mechanophore incorporated feedstocks for additive manufacturing. Materials Today Communications. 34: 105525, 2023.
8. M. Seydibeyoglu, A. Dogru, J. Wang, M. Rencheck, Y. Han, L. Wang, E. Seydibeyoglu, X. Zhao, K. Ong, J. Shatkin, S. Es-haghi, S. Bhandari, S. Ozcan, D. Gardner. Review on hybrid reinforced polymer matrix composites with nanocellulose, nanomaterials, and other fibers. Polymers. 15 (4): 984, 2023.
9. S. Bhagia, S. Kore, S. Wasti, J. Durkovic, J. Kovac, X. Zhao, H. Andrews, M. Martin, N. Gallego, U. Vaidya, S. Ozcan. 3D printing of a recycled copolyester of terephthalic acid, cyclohexanedimethanol and tetramethylcyclobutanediol. Polymer Testing. 118: 107916, 2023.
10. K. Li, Y. Li, H. Tekinalp, V. Kumar, X. Zhao, Y. Pu, A. Ragauskas, K. Nawaz, T. Aytug, S. Ozcan. Hydrogen bond–induced aqueous-phase surface modification of nanocellulose and its mechanically strong composites. Journal of Materials Science. 57 (17): 8127-8138, 2022.
11. M. Lamm, K. Li, D. Ker, X. Zhao, H. Hinton, K. Copenhaver, H. Tekinalp, S. Ozcan. Exploiting chitosan to improve the interface of nanocellulose reinforced polymer composites. Cellulose. 29 (7): 3859-3870, 2022.
12. K. Copenhaver, K. Li, M. Lamm, C. Walker, D. Johnson, Y. Han, L. Wang, X. Zhao, Y. Pu, H. Hinton, H. Tekinalp, S. Bhagia, A. Ragauskas, D. Gardner, S. Ozcan. Recycled cardboard containers as a low energy source for cellulose nanofibrils and their use in poly(l-lactide) nanocomposites. ACS Sustainable Chemistry & Engineering. 9 (40): 13460-13470, 2021.
13. S. Bhagia, K. Bornani, R. Agarwal, A. Satlewal, J. Ďurkovič, R. Lagaňa, M. Bhagia, C. Yoo, X. Zhao, V. Kunc, Y. Pu, S. Ozcan, A. Ragauskas. Critical review of FDM 3D printing of PLA biocomposites filled with biomass resources, characterization, biodegradability, upcycling and opportunities for biorefineries. Applied Materials Today. 24: 101078, 2021.
14. K. Li, D. Mcgrady, X. Zhao, D. Ker, H. Tekinalp, X. He, J. Qu, T. Aytug, E. Cakmak, J. Phipps, S. Ireland, V. Kunc, S. Ozcan. Surface-modified and oven-dried microfibrillated cellulose reinforced biocomposites: cellulose network enabled high performance. Carbohydrate Polymers. 256: 117525, 2021.
15. L. Wang, D. Gardner, J. Wang, Y. Yang, H. Tekinalp, M. Tajvidi, K. Li, X. Zhao, D. Neivandt, Y. Han, S. Ozcan, J. Anderson. Towards the scale-up production of cellulose nanocomposites using melt processing: a critical review on structure-processing-property relationships. Composites Part B: Engineering. 201: 108297, 2020.
16. Y. Wang, K. Li, X. Zhao, H. Tekinalp, T. Li, S. Ozcan. Toughening by nanodroplets: polymer-droplet biocomposite with anomalous toughness. Macromolecules. 53 (11): 4568-4576, 2020.
17. K. Li, Y. Wang, M. Rowe, X. Zhao, T. Li, H. Tekinalp, S. Ozcan. Poly(lactic acid) toughening through chain end engineering. ACS Applied Polymer Materials. 2: 411-417, 2020.
18. ORNL’s Website of Manufacturing Demonstration Facility (MDF) (opens in new window)